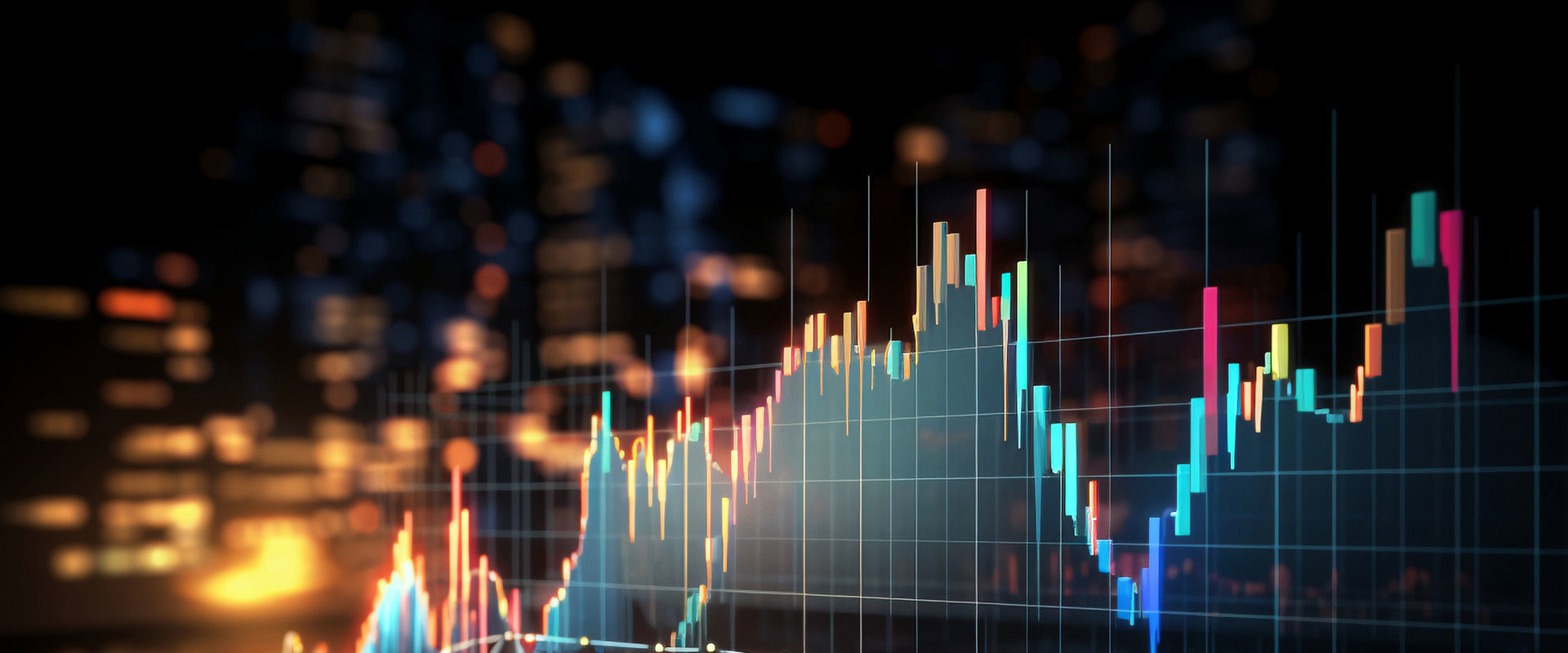
Technical Requirements for Investment Casting
Throughout the production process, precision casting immediately solidifies its liquid at room temperature, and then pours the compound into its unique mold casting medium level. Precision casting is easily affected by solids, and then immediately heats up to liquid metal materials. The composite materials used include lead, copper, iron, aluminum, etc.
Metal materials, sand or pottery can be used as raw materials for mold casting in precision casting. In the whole process of use, different methods must be used according to their different requirements. This production manufacturing method is called cast iron parts, and its metal material type can be gray iron or gray cast iron.
Investment casting cylinder plug can be machining process, precision casting can produce and manufacture its complex appearance parts, especially the complex inner wall blank. In the process of mining machinery investment casting, the application range is very wide. Generally speaking, metal composite materials commonly used in industrial production can be calcined.
The source of raw materials for precision casting is very wide, and the product is very cheap throughout the use process. The appearance, specifications and parts of old parts, scrap steel and cut castings of mechanical equipment are very close, which can reasonably reduce the amount of milling, and generally belong to non-milling production.
The production and manufacture of many precision castings reasonably set favorable specifications for the casting of processing plants. In the whole application process, a very powerful technical modeling design method is used. The air-flush design line of the product can be integrated into the requirements of fast and high-precision modeling design and production line, and the core-making method can adopt efficient core-making methods such as shell core.
The pouring temperature and pouring rate of stainless steel coated sand casting should be strictly controlled. So the operation steps of pouring stainless steel castings
1. Pouring temperature. Different pouring temperatures have a great influence on the quality of stainless steel castings. Therefore, we should create a suitable pouring temperature according to the aluminum alloy type, cast iron structure and metal casting characteristics of stainless steel castings. Generally speaking, the pouring temperature established by each person when pouring stainless steel castings should be between 1540-1580 ℃;
2. Pouring rate. The speed of pouring is related to the speed of forming stainless steel castings. Therefore, we should choose stainless steel castings with different specifications, and the pouring speed is different under the specification that ensures the relatively smooth discharge of the cavity gas. Generally speaking, we should choose the fast pouring rate of stainless steel castings, and the completion sequence solidification of stainless steel castings, we should choose the slower pouring rate;
3. Everyone is pouring big. Pay attention to small and medium-sized stainless steel castings, the liquid steel must be placed for 2 minutes before pouring;
4. After the stainless steel casting is successfully poured, the press iron and the box card must be removed immediately after the cast iron is solidified, otherwise the stainless steel casting will have cracks.
Related News
2024/09/11
What is the function of the valve body?
The valve body is the main component of the valve body, and there are different mechanical manufacturing methods according to the pressure level.
View Details